All about Manufacturings
Wiki Article
The Buzz on Additive Manufacturing
Table of ContentsAn Unbiased View of Lean ProductionGetting My Manufacturing To WorkThe Only Guide for Manufacturing IndustriesOur Mfg IdeasSome Known Details About Mfg Our Additive Manufacturing Ideas
The message on this page is a sample from our complete White Paper 'Shot Moulding for Customers' - * Example text * - for complete overview click the download switch above! Intro This overview is meant for people who are seeking to source plastic mouldings. It offers a much needed insight right into all that is included with developing plastic components, from the mould device called for to the moulding process itself.If you wish to discover even more, the guide covers kinds of mould tools, as well as unique completing procedures such as colours & plating. Words that are highlighted can be found in the reference in the appendix ... Part I: Moulding: The Basics The Benefits of Injection Moulding Plastic shot moulding is an extremely exact procedure that provides several benefits over other plastic processing methods.
Accuracy is ideal for extremely elaborate parts. You can hold this moulding in the palm of your hand as well as it has managers, ribs, steel inserts, side cores and also openings, made with a gliding closed off feature in the mould tool.
All About Plastic Manufacturing

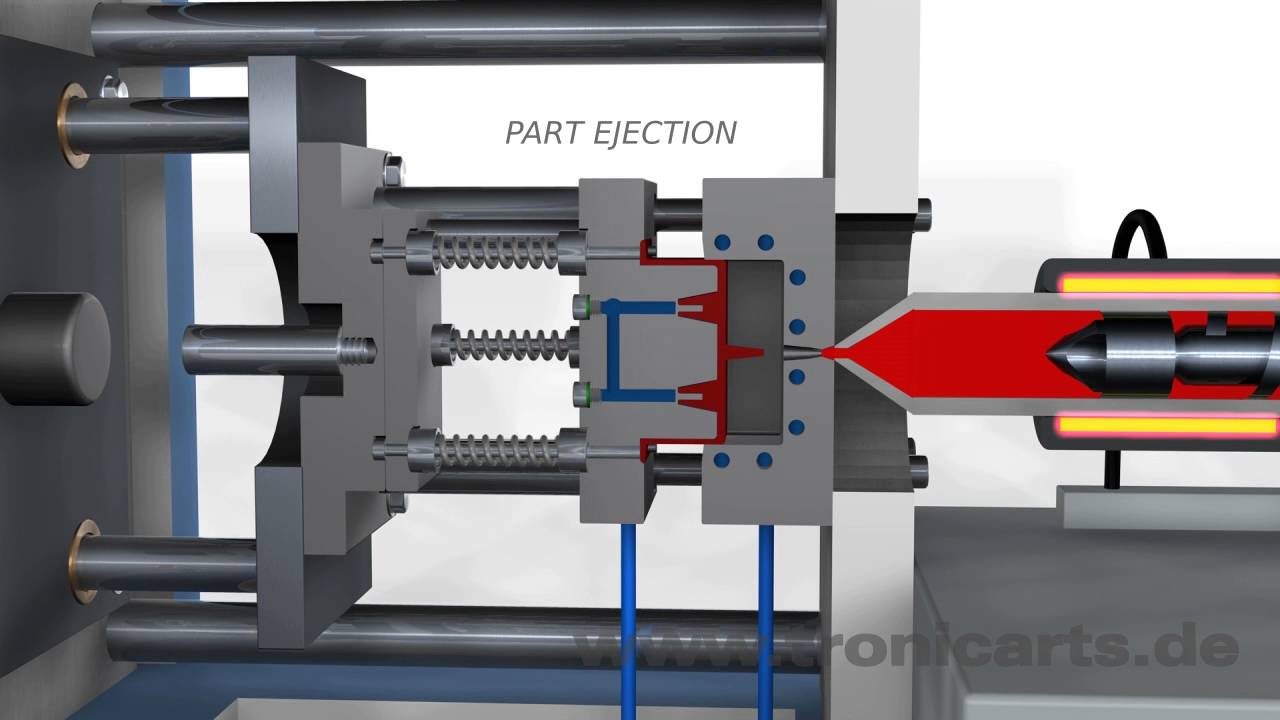
Everything about Plastic Manufacturing
from material feed Product melting; material injection; shot time cooling down ejection and also the re-closing of the mould tool ready for the next cycleFollowing Draft angles - The wall surfaces of a moulded component should be a little tapered in the direction in which the part is expelled from the mould device, to allow the component to be ejected quickly.Ejector stroke - The pressing out of ejector pins to eject the moulded component from the mould tool. Ejector stroke rate, length as well as timing requires to be thoroughly managed to stop damages to the ejectors and also mould device, but at the very same time make the moulding cycle as short as feasible.
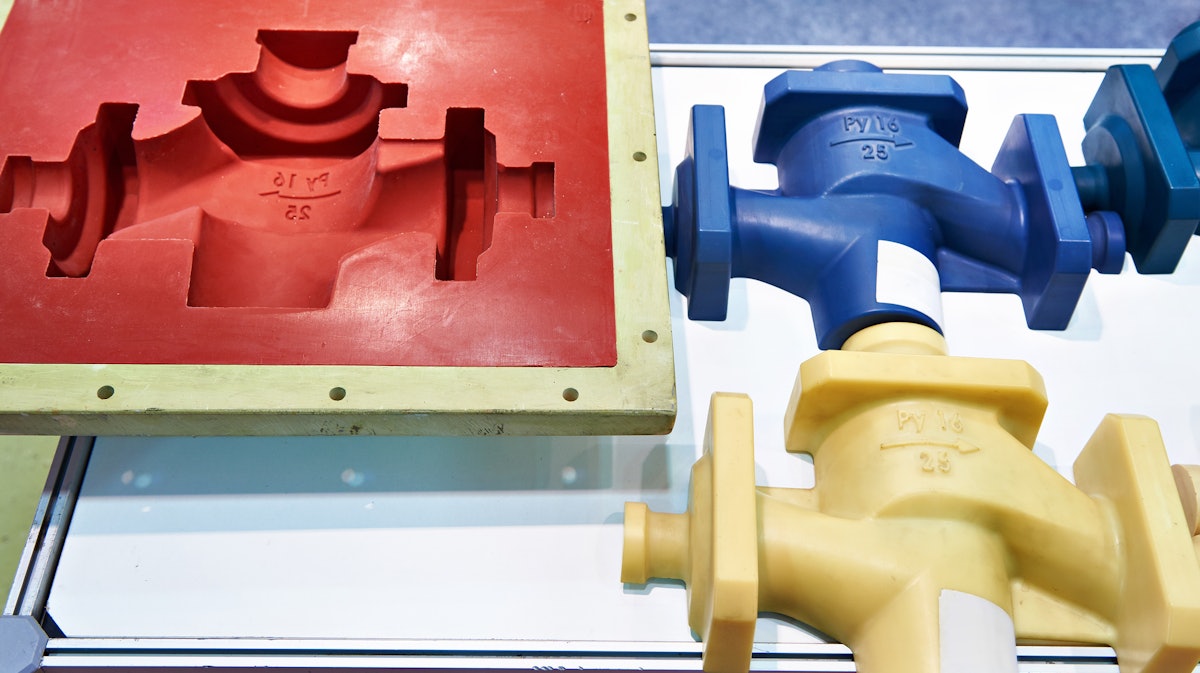
Excitement About Lean Production
Ribs - When a plastic component has slim walls, ribs are contributed to the layout to make the slim wall surfaces stronger Side cores - Side activity which generates a feature on a moulded part, at an opposing angle to the normal opening instructions of the mould tool. mfg. The side core requires to be able to retract as the plastic part can not be expelled otherwise.
Walls - The sides of a moulded part The message on this web page is an example from our complete White Paper 'Injection Moulding for Purchasers'.
Manufacturing process for producing components by infusing liquified product into a mould, or mold and mildew Streamlined representation of the process Injection moulding (U.S. spelling: shot molding) is a production process for producing components by infusing molten material into a mould, or mold and mildew. Injection moulding can be carried out with a host of products mostly including metals (for which the process is called die-casting), glasses, elastomers, confections, and the majority have a peek here of generally thermoplastic as well as thermosetting polymers. Shot moulding is commonly utilized for manufacturing a selection of components, from the tiniest parts to whole body panels of autos. Advancements in 3D printing innovation, using photopolymers that do not melt during the injection moulding of some lower-temperature thermoplastics, can be used for some straightforward shot moulds. Injection moulding makes use of a special-purpose equipment that has 3 components: the injection unit, the mould and the clamp.
The Main Principles Of Manufacturing
, with the volume used of the former being significantly higher.: 13 Thermoplastics are widespread due to qualities that make them very suitable for shot moulding, such as convenience of recycling, flexibility for a broad variety of applications,: 89 and ability to soften as well as stream on home heating.In several tooth cavity moulds, each dental caries can be the same and also form the exact same components or can be one-of-a-kind and develop numerous different geometries during a single cycle.
When enough material has actually collected, the material is compelled at high stress and speed jit manufacturing into the component forming dental caries. The precise quantity of contraction is a function of the resin being used, and also can be relatively foreseeable. To avoid spikes in pressure, the procedure typically uses a transfer setting matching to a 9598% full cavity where the screw changes from a consistent velocity to a consistent pressure control.
The Of Lean Production
When the screw gets to the transfer setting the packaging pressure is applied, which completes mould filling as well as makes up for thermal contraction, which is rather high for thermoplastics about lots of other products. The packing stress is applied until eviction (tooth cavity entryway) strengthens. As a result of its little dimension, eviction is generally the starting point to solidify through its entire thickness.: 16 Once the gate read here strengthens, no more product can enter the tooth cavity; appropriately, the screw reciprocates and also gets product for the following cycle while the product within the mould cools down to ensure that it can be expelled as well as be dimensionally stable.Report this wiki page